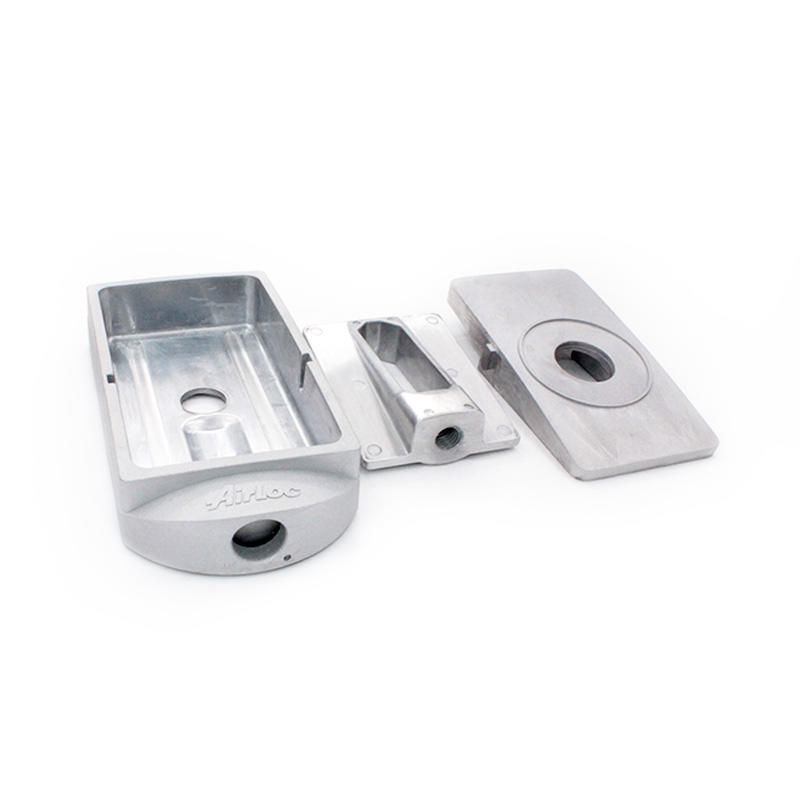
Impact Of Custom Aluminum Die Casting In Today’s Scenario
The advancing world has created many opportunities and modifications in daily life. We can come across more advanced products in every field with better functionality and features working towards bringing efficiency in everything they fit. The same is correct for building materials, such as aluminum, iron, steel, and other alloys. People have devised multiple ways and processes to change the physical state of these building materials towards better and efficient products. Custom Aluminium die casting is one of those processes that intensifies its efficiency by modifying its existing properties for better building materials. Hence, let us understand various aspects of the process.
What is aluminum die casting?
Aluminum die casting is a process that involves high pressure to molten aluminum or aluminum alloys to produce defined, smooth, custom, textured surface parts of efficient and desired shapes and sizes. Custom aluminum die casting follows a series of subsequent steps that eventually yields products with higher functionality. The process can be either a hot chamber or cold chamber die casting, but the high melting point of aluminum at about 1150 degrees prefers the latter method.
How does the die casting process go?
The aluminum die casting process involves a steel mold that yields more modified products in no time. It begins with molten aluminum under high pressure. Then a die casting press with two die halves tightly clamped receives molten aluminum into the die cavity. After some time, the molten aluminum in the die casting cavity solidifies, after which the final product ejection takes on drawing apart from the die halves of the press. In this way, the aluminum die casting method produces aluminum products of customized shapes, sizes, and textures.
Where can we use aluminum die-casted products?
Aluminum die-casted products have multiple uses in the metal industry. The process modifies the properties of aluminum and makes the final product with distinctive features, such as lightweight, corrosion-resistant, high thermal, and electrical conductance. We get more durable, cost-effective, corrosion-resistant, highly conductive, lightweight, and recyclable materials. These are the main advantages of the aluminum die casting process. Products with such characteristics find application in the building industry as replacements for iron and steel components in building partitions, handheld devices, vehicles, and much more.
Hence, considering various aspects of the aluminum die casting process, we can conclude that it is vital and versatile in the metal industry, the way for better and advanced products.